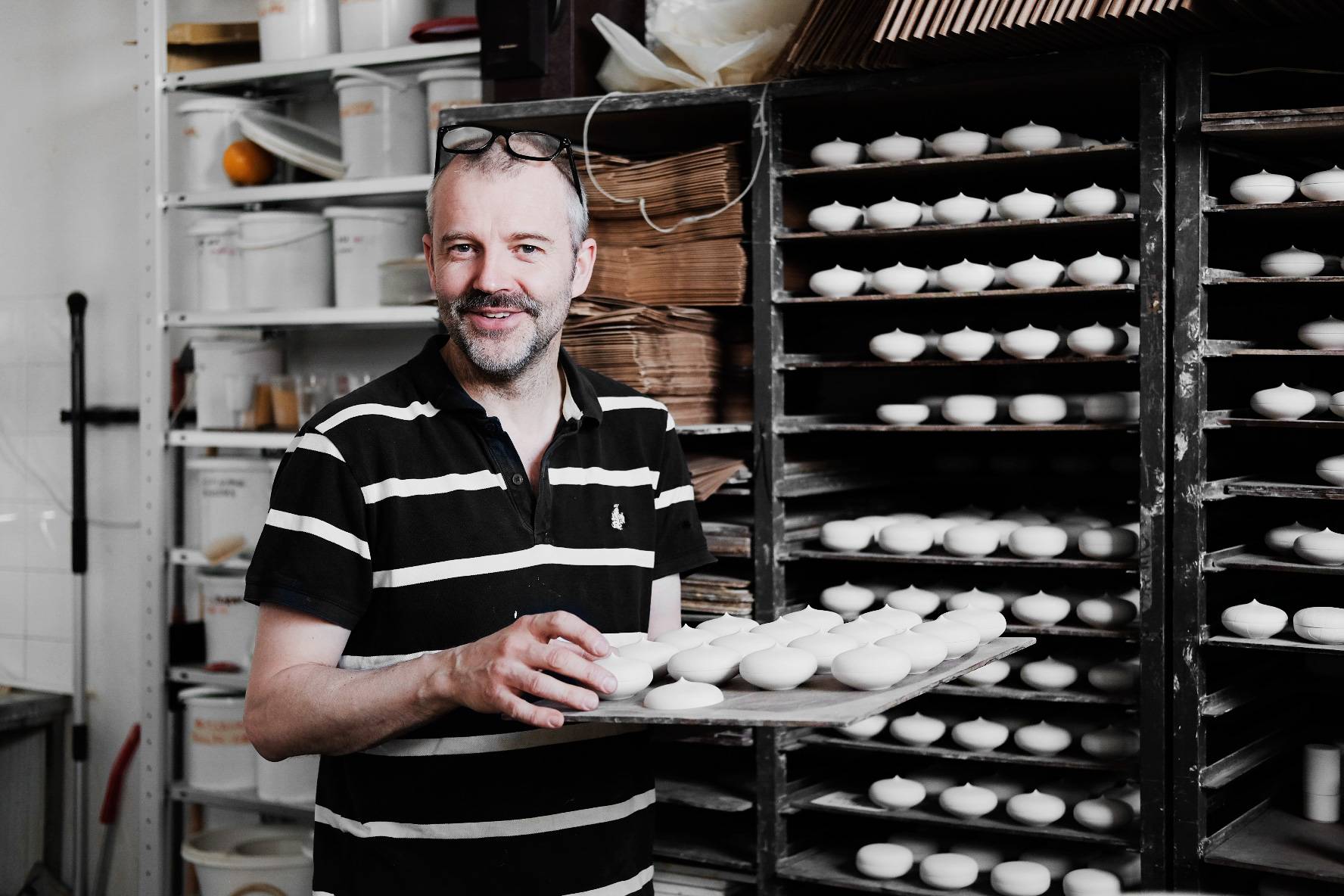
Möte med Jonas Lindholm
I Gustavsbergs porslinsfabriks före detta lokaler i Gustavsberg på Värmdö utanför Stockholm har Jonas Lindholm sin ateljé. Jonas flyttade in 1994 och var en av de första fristående keramikerna som flyttade in i lokalerna efter att porslinsfabriken minskat sin produktion.
I Gustavsbergs porslinsfabriks före detta lokaler i Gustavsberg på Värmdö utanför Stockholm har Jonas Lindholm sin ateljé. Jonas flyttade in 1994 och var en av de första fristående keramikerna som flyttade in i lokalerna efter att porslinsfabriken minskat sin produktion.
Creating a functional ceramic object involves several steps. Most of Jonas's products are made through casting. The first step in this process is creating a mold. Jonas models the desired final product and then casts a plaster mold based on that model. Typically, a product consists of several parts that require separate plaster molds, and all the different parts are assembled after casting.
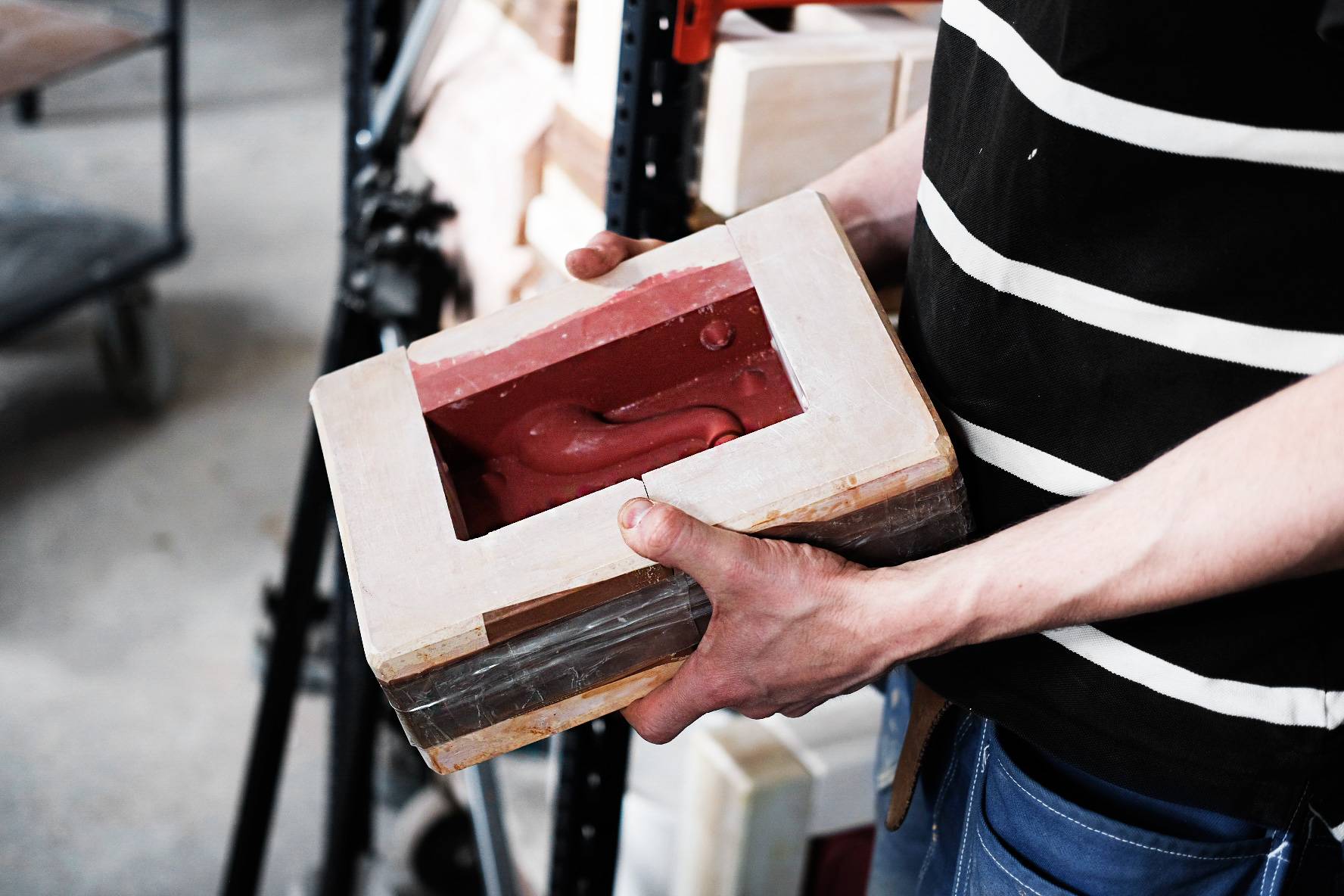
The liquid stoneware clay is prepared, sieved, and poured into the plaster mold. After a layer of clay has solidified in the mold, the remaining liquid clay is poured out. Once the remaining clay has fully solidified, the mold is opened, and the product is removed. Then, it undergoes a light polishing using a sponge or fine steel wool.
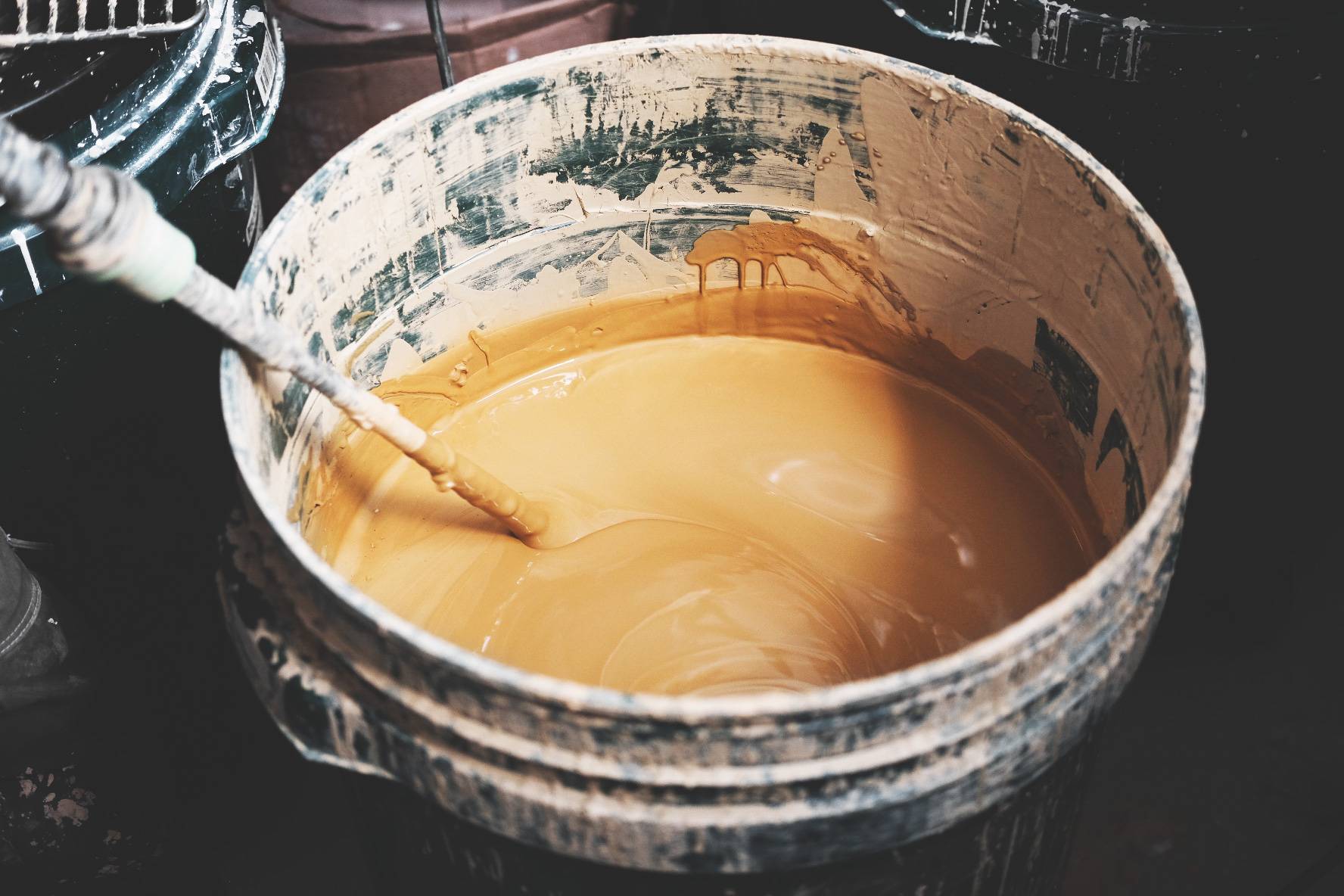
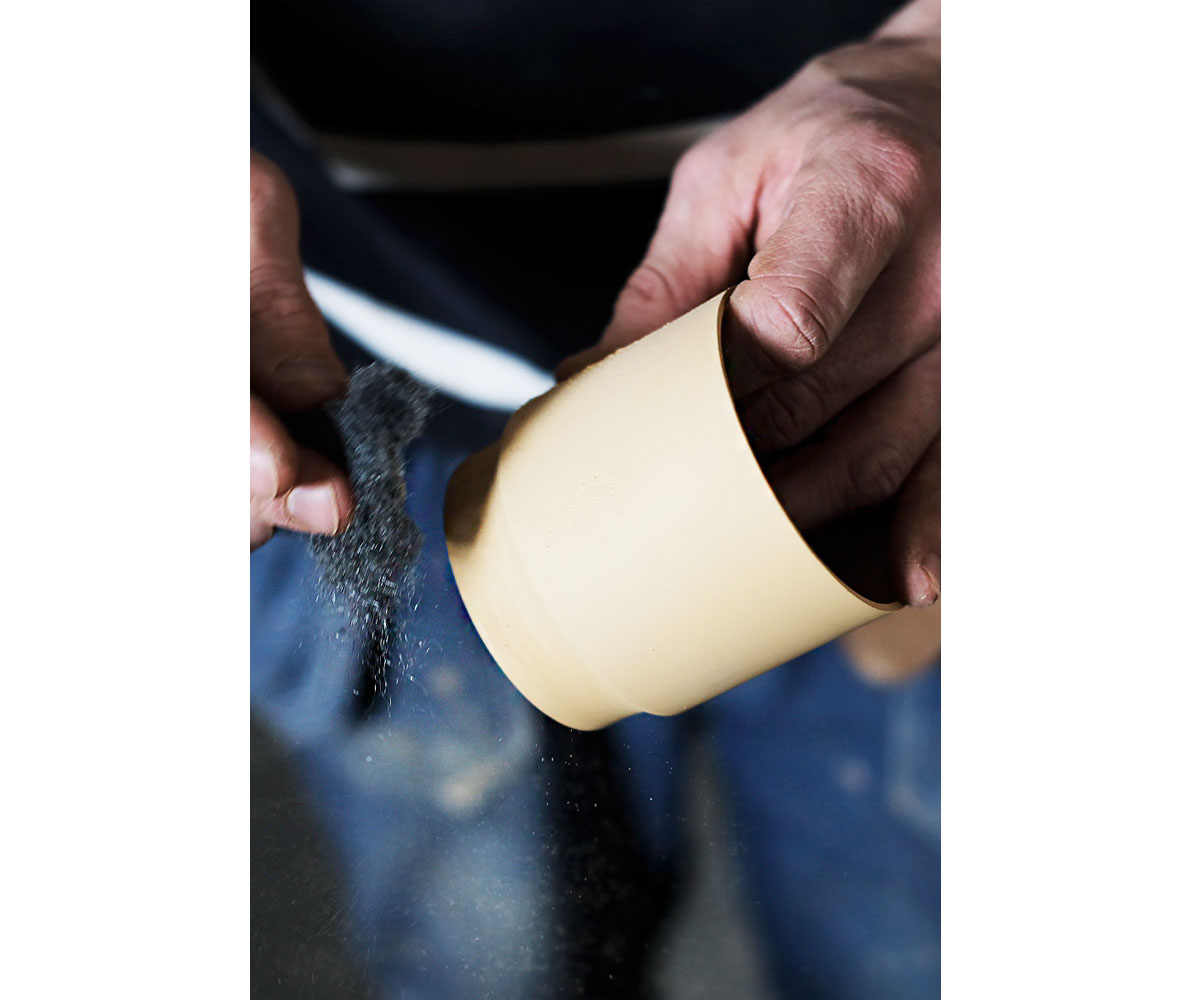
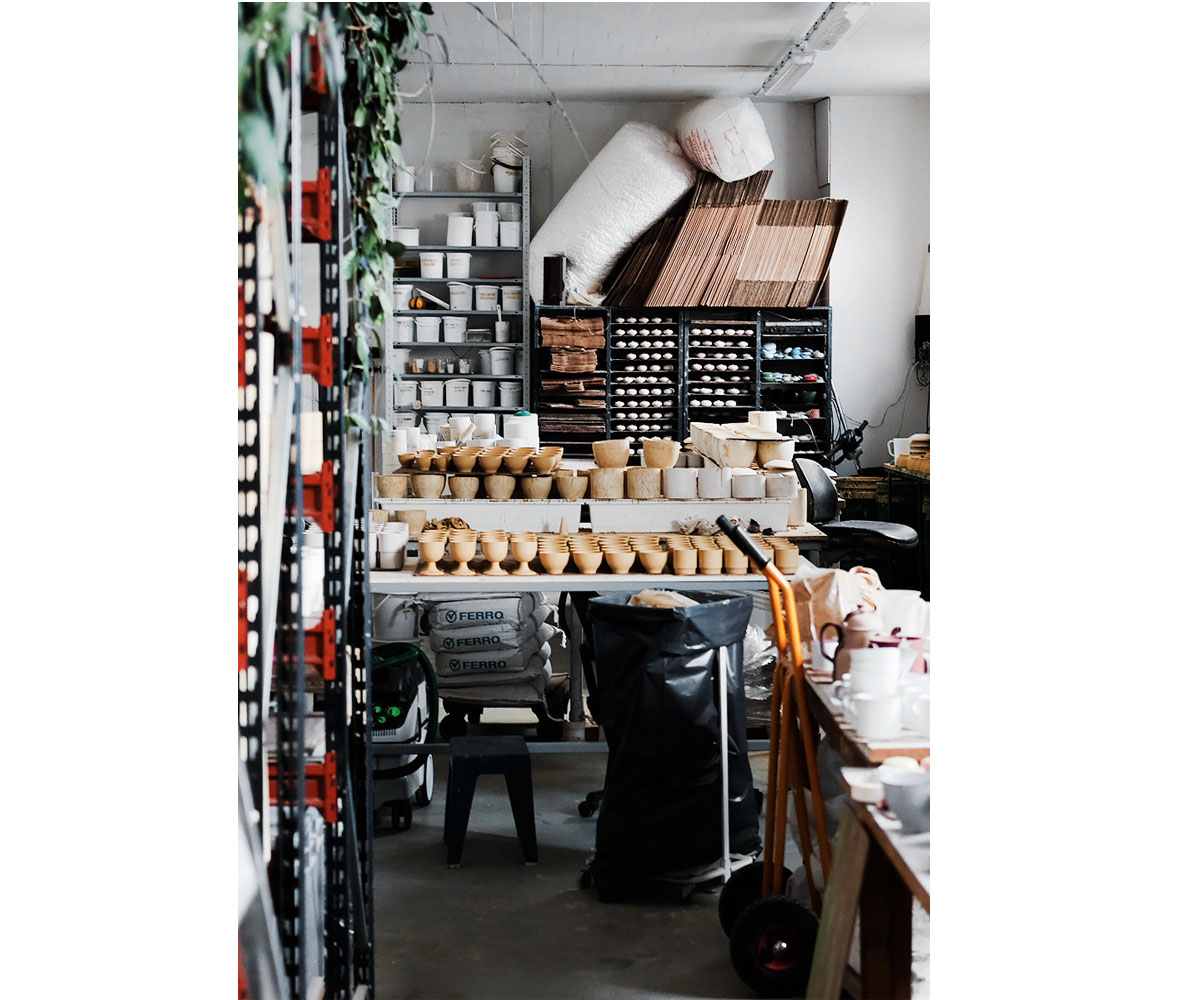
The next step is called bisque firing, a process where the clay is fired to make it less brittle and easier to handle. The ceramics are placed in a bisque kiln for approximately 10-12 hours, gradually raising the temperature until it reaches a peak of about 920 degrees Celsius.
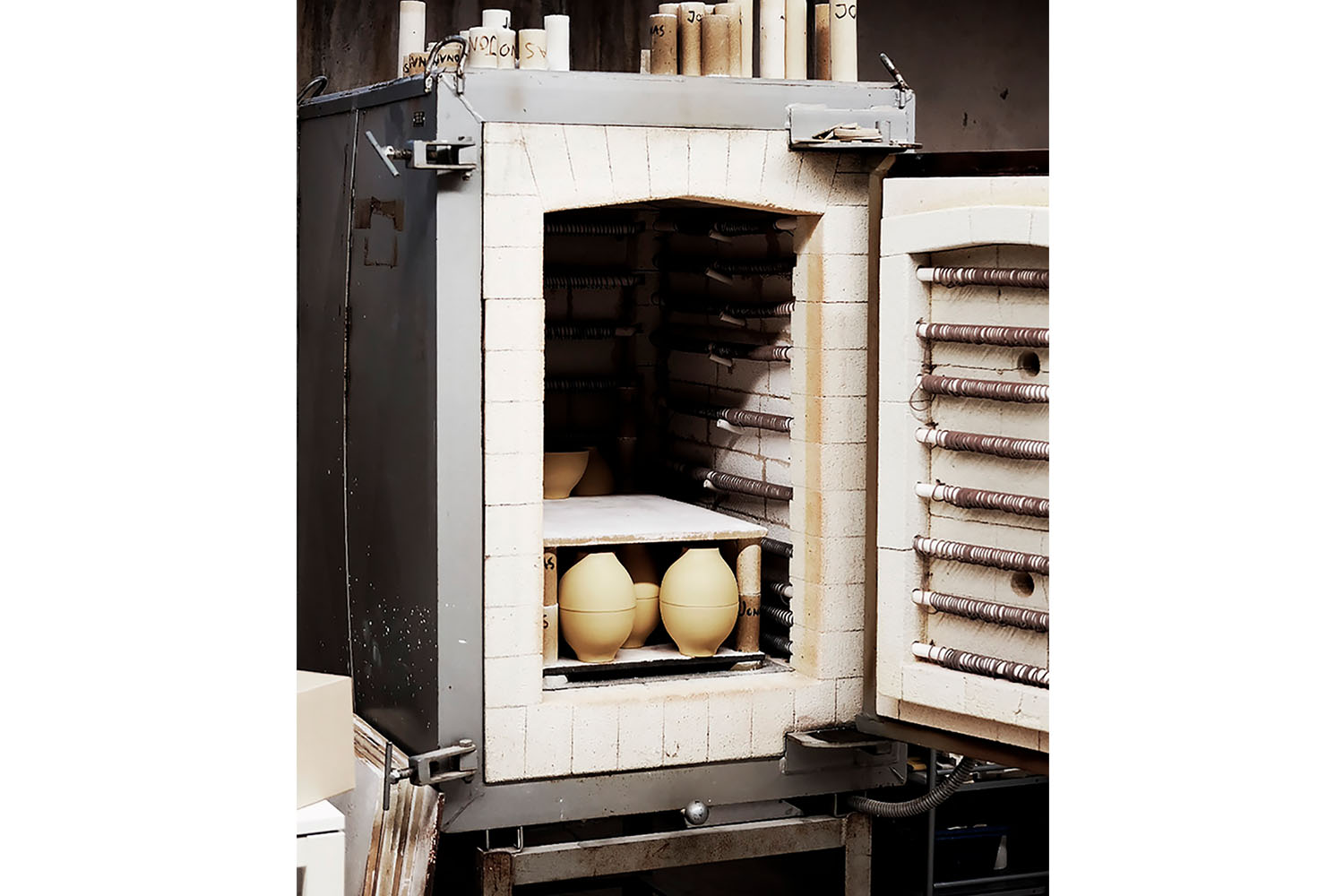
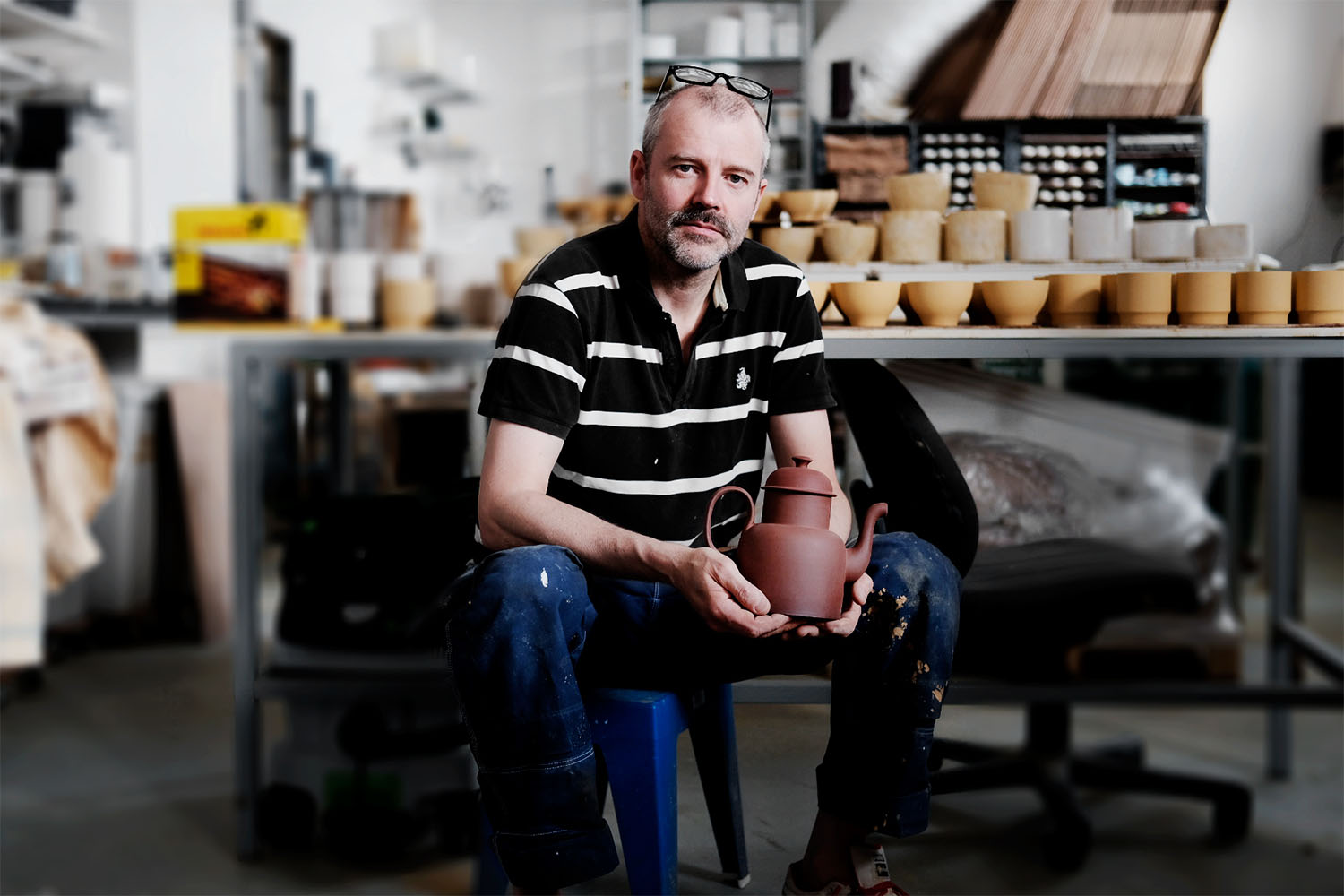
The final step is glaze firing, where the product is dipped in glaze and placed back in the kiln until the glaze melts. The temperature during glaze firing reaches approximately 1200 degrees Celsius. The ceramics remain in the kiln for another 10-12 hours. Once the kiln has cooled down, the finished products are removed and ready for sale.
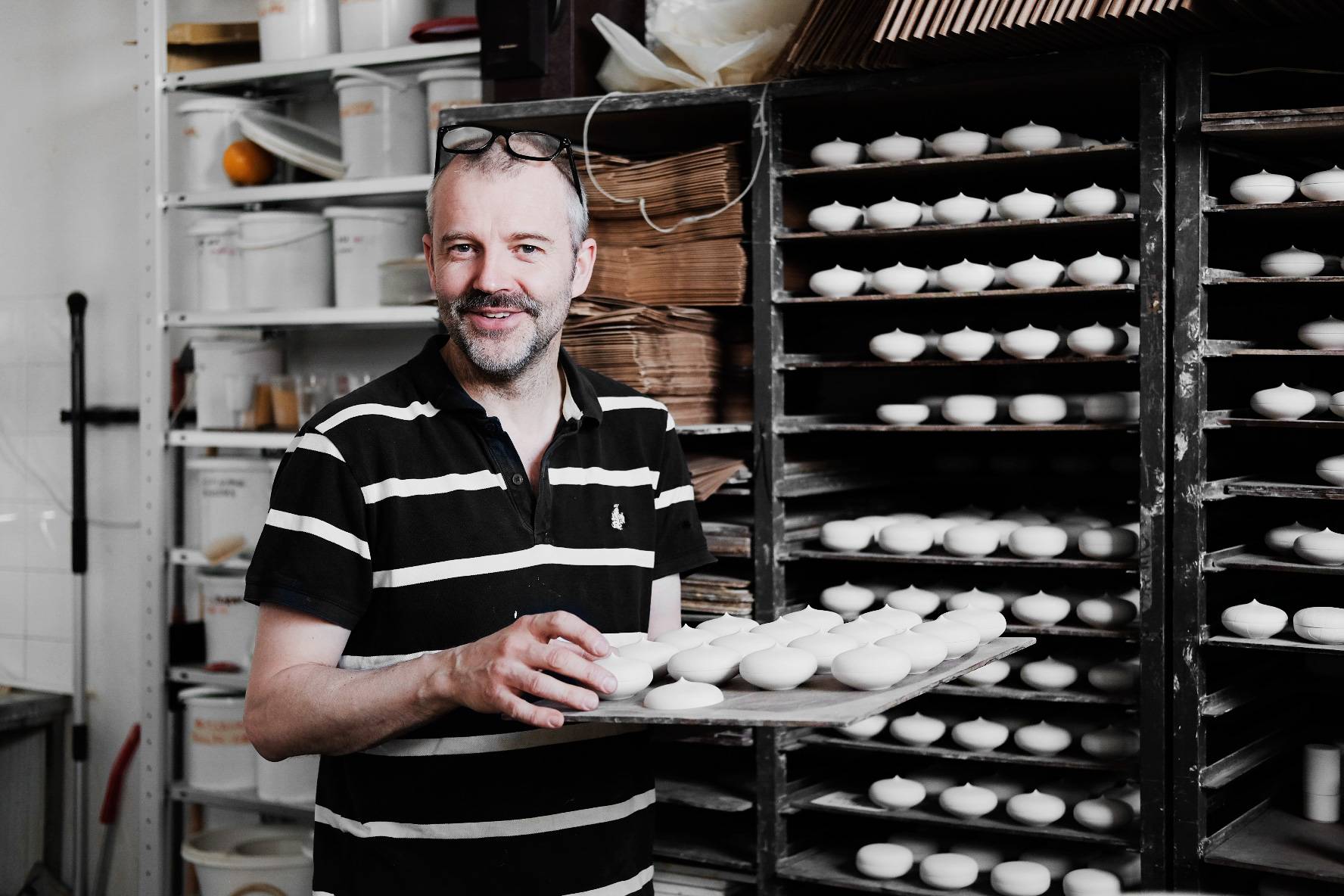
Visit at Jonas Lindholm
In the former premises of Gustavsberg Porcelain Factory in Gustavsberg, located in Värmdö outside Stockholm, Jonas Lindholm has his studio. Jonas moved in 1994 and was one of the first independent ceramicists to occupy the space after the porcelain factory reduced its production.
In the former premises of Gustavsberg Porcelain Factory in Gustavsberg, located in Värmdö outside Stockholm, Jonas Lindholm has his studio. Jonas moved in 1994 and was one of the first independent ceramicists to occupy the space after the porcelain factory reduced its production.
Creating a functional ceramic object involves several steps. Most of Jonas's products are made through casting. The first step in this process is creating a mold. Jonas models the desired final product and then casts a plaster mold based on that model. Typically, a product consists of several parts that require separate plaster molds, and all the different parts are assembled after casting.
The liquid stoneware clay is prepared, sieved, and poured into the plaster mold. After a layer of clay has solidified in the mold, the remaining liquid clay is poured out. Once the remaining clay has fully solidified, the mold is opened, and the product is removed. Then, it undergoes a light polishing using a sponge or fine steel wool.
The liquid stoneware clay is prepared, sieved, and poured into the plaster mold. After a layer of clay has solidified in the mold, the remaining liquid clay is poured out. Once the remaining clay has fully solidified, the mold is opened, and the product is removed. Then, it undergoes a light polishing using a sponge or fine steel wool.
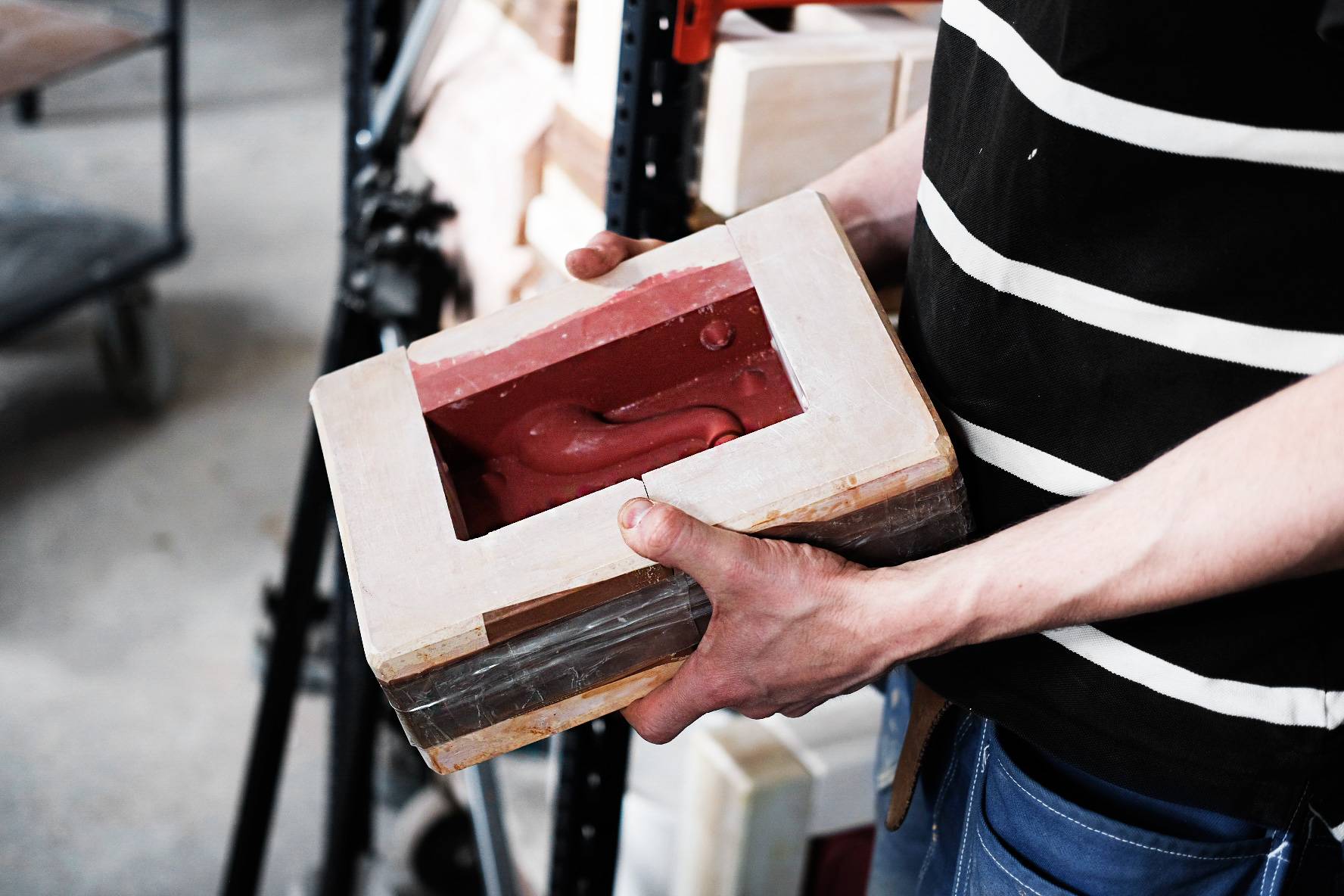
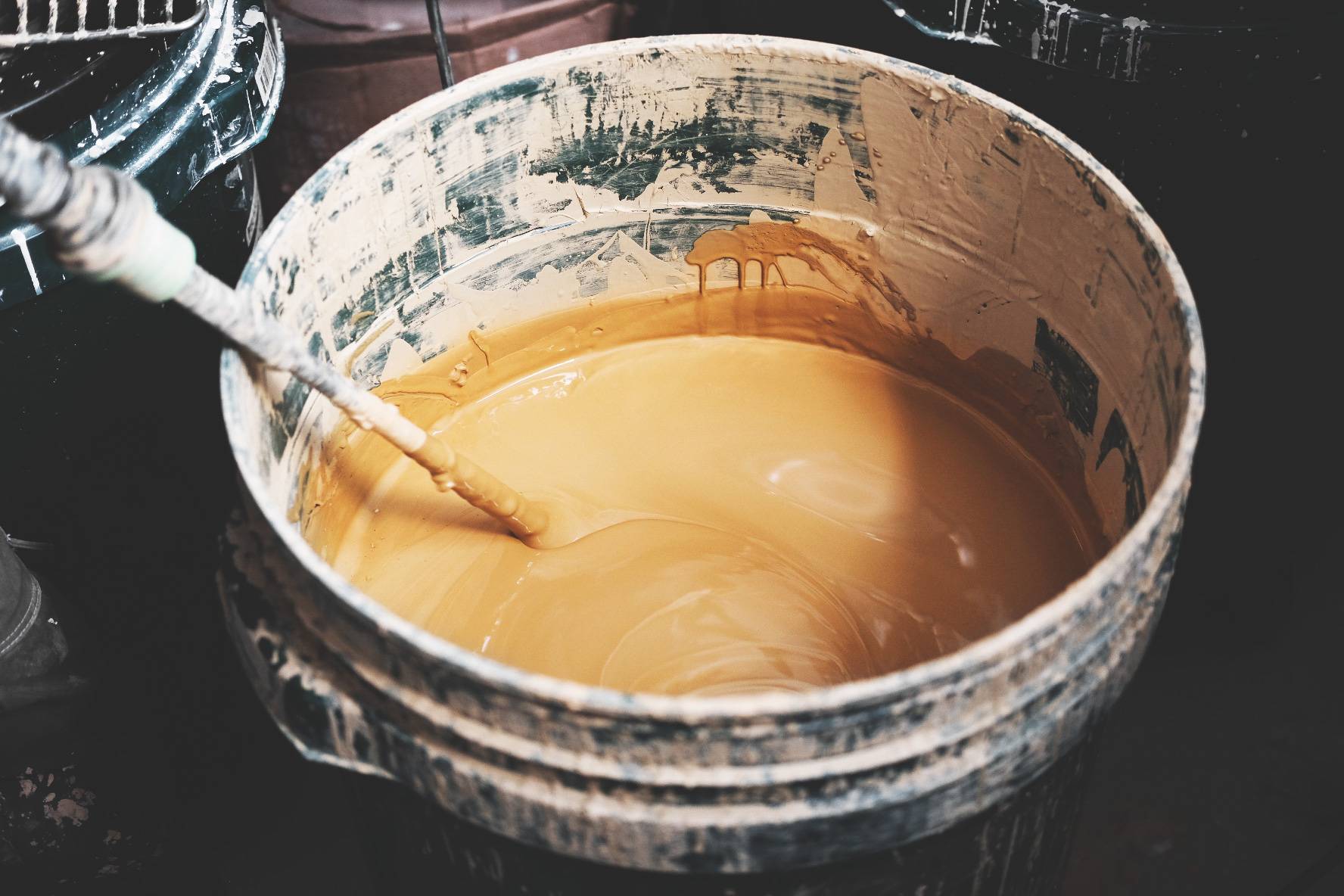
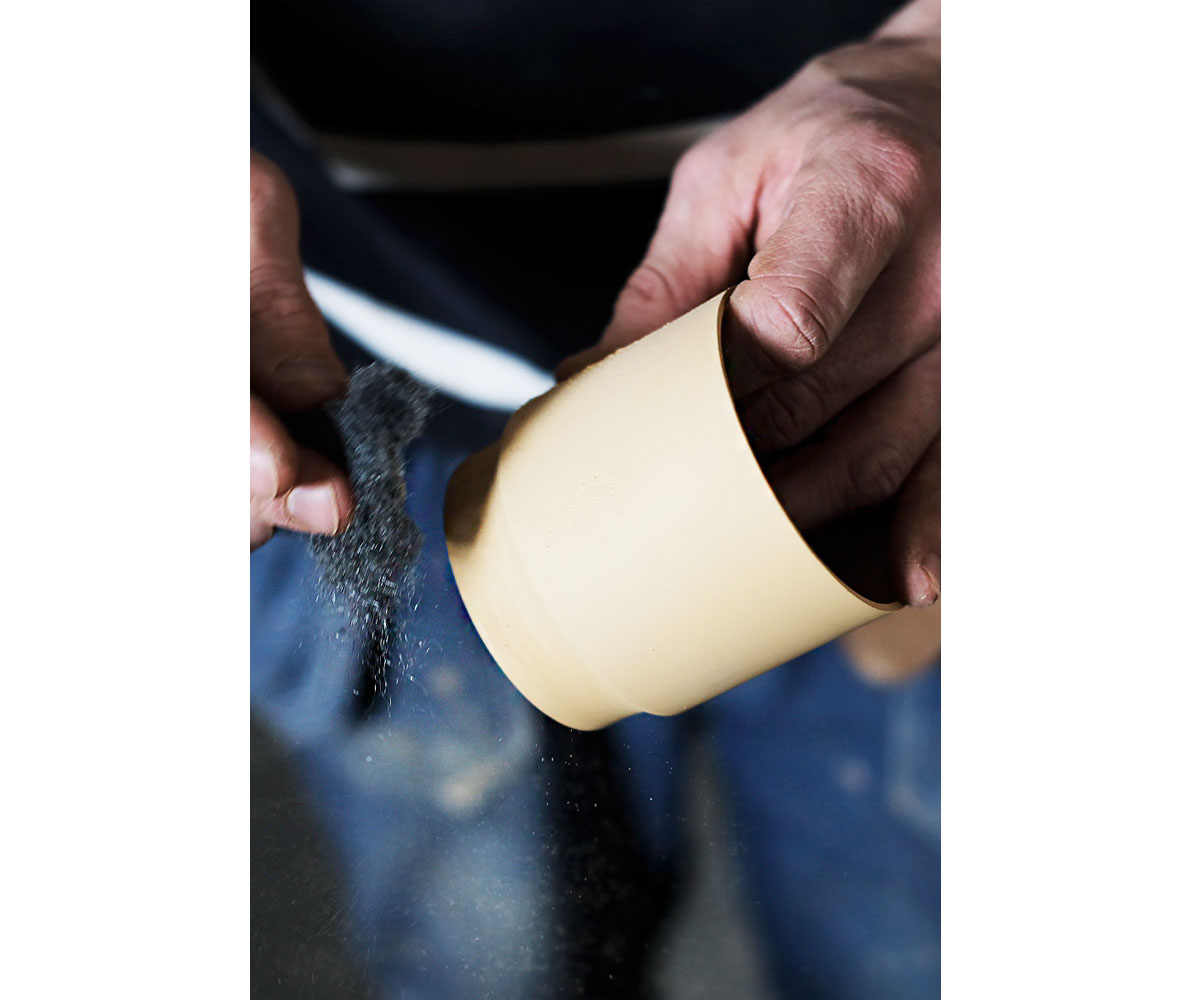
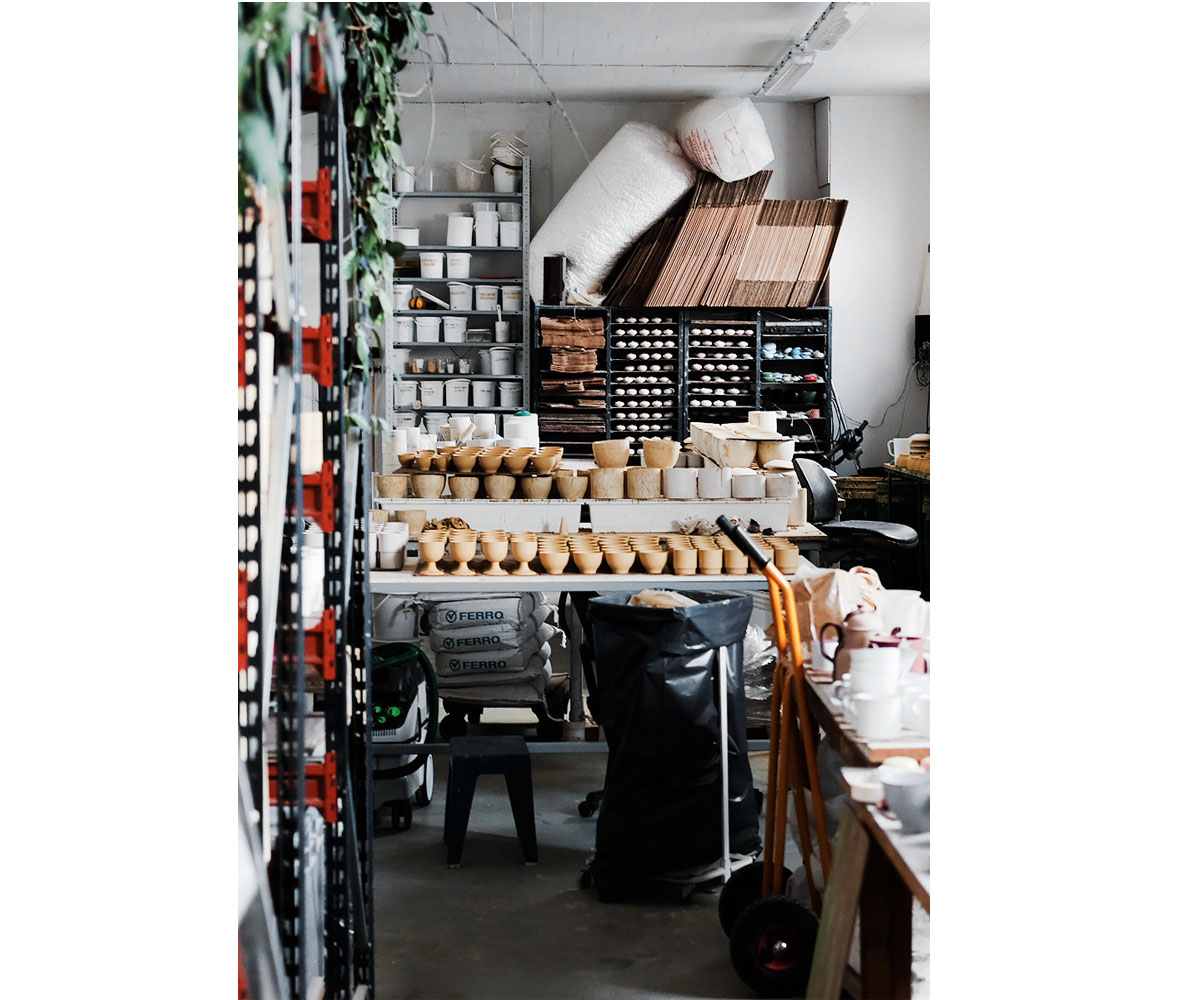
The next step is called bisque firing, a process where the clay is fired to make it less brittle and easier to handle. The ceramics are placed in a bisque kiln for approximately 10-12 hours, gradually raising the temperature until it reaches a peak of about 920 degrees Celsius.
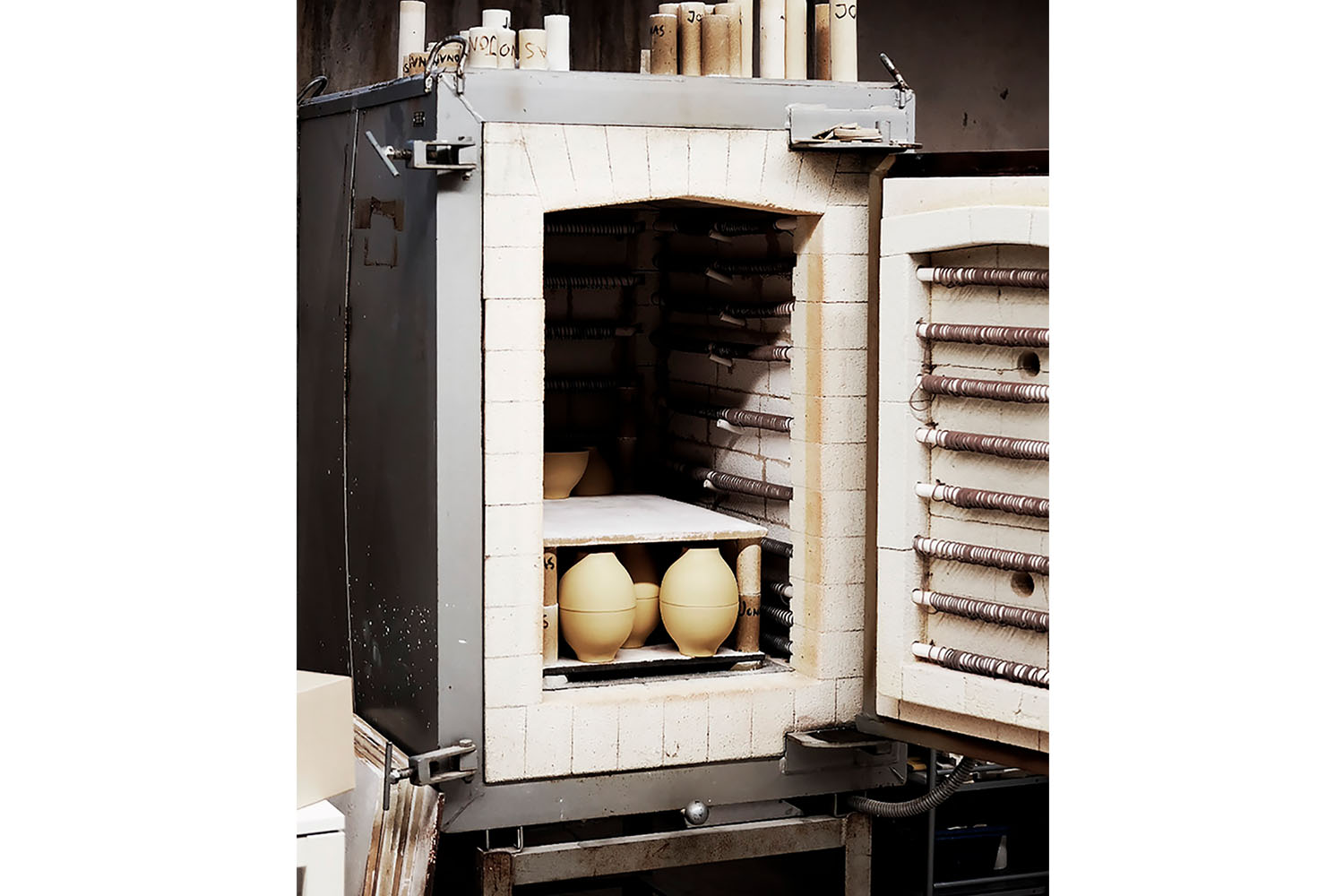
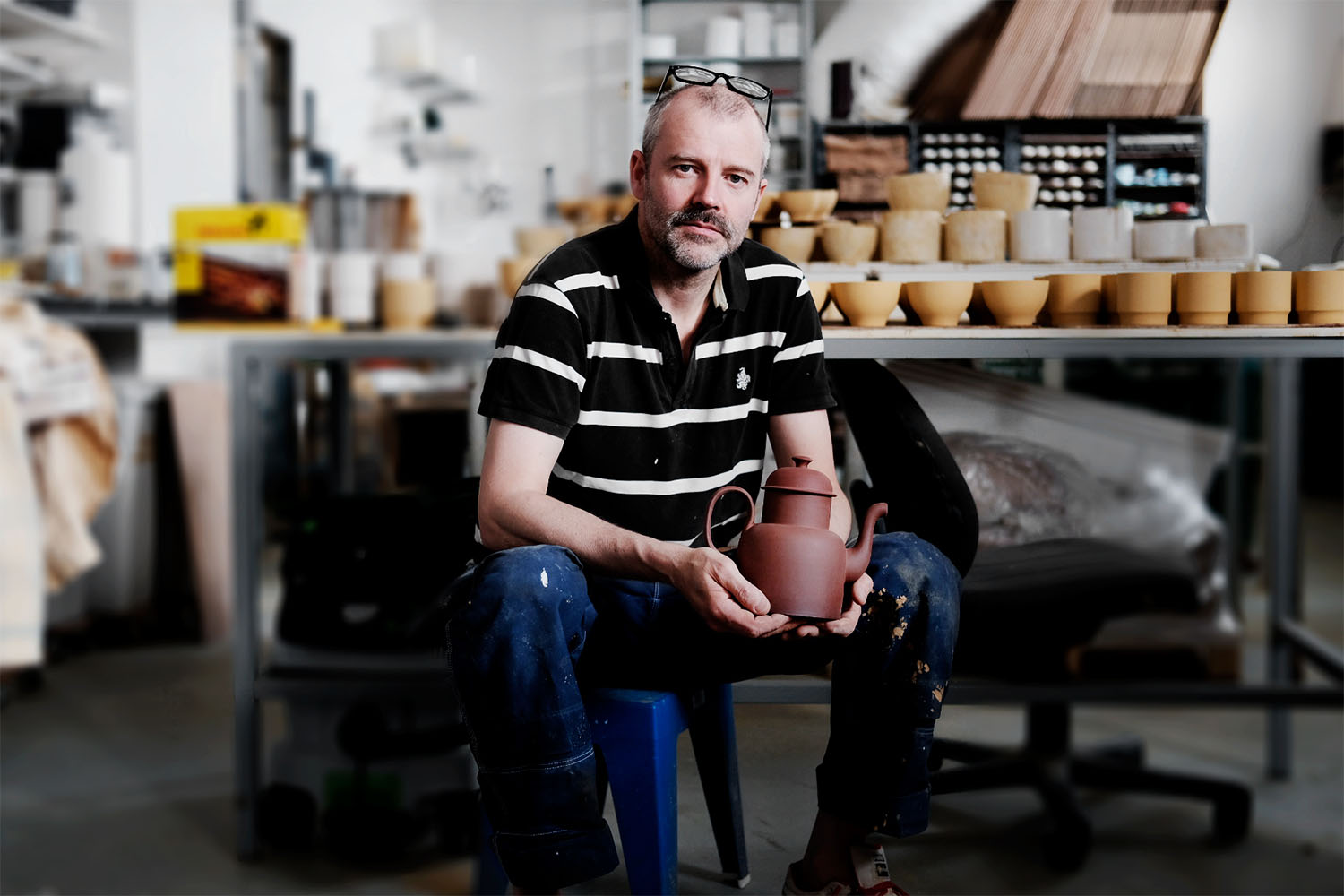
The final step is glaze firing, where the product is dipped in glaze and placed back in the kiln until the glaze melts. The temperature during glaze firing reaches approximately 1200 degrees Celsius. The ceramics remain in the kiln for another 10-12 hours. Once the kiln has cooled down, the finished products are removed and ready for sale.
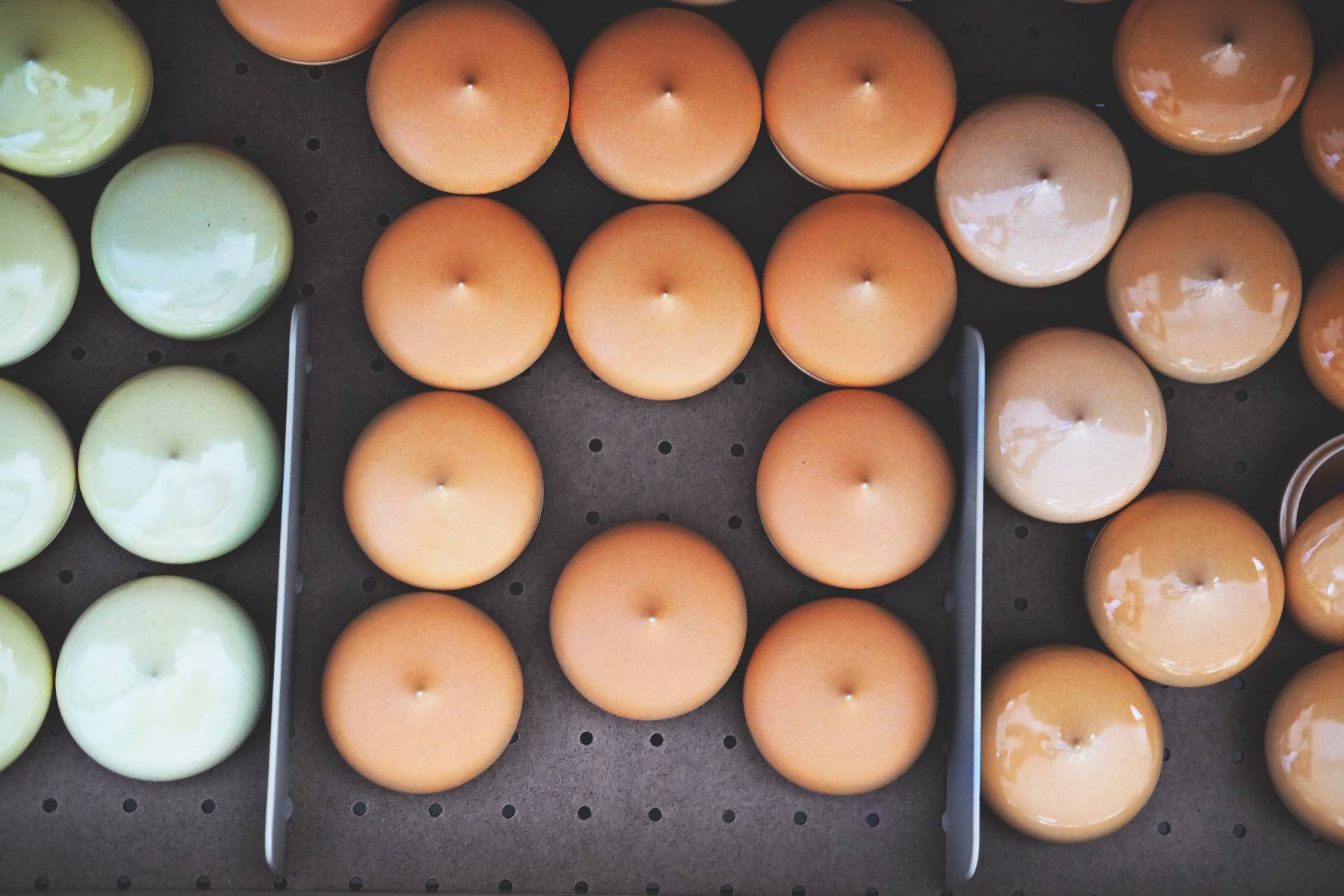
Selected Products